Wood vs Concrete, a Material Perspective
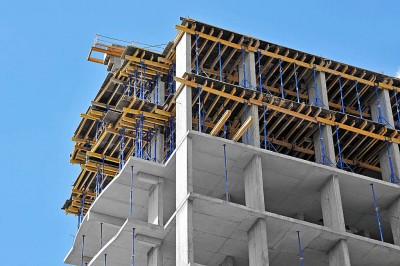
Wood vs Concrete, a Material Perspective: Cement Association of Canada
This is an excerpt from an article found in Building Magazine about the difference between Concrete or Wood with construction. The good news is that there’s an AccuCrete® product that will work regardless of the base product!
Interview with: Adam Auer, Vice President, Environment and Sustainability and Richard J. McGrath, Director Codes and Standards – Buildings
Overview on Concrete high-rise construction in Canada
Concrete is often seen as an “old” if proven technology for residential and commercial construction over six stories. How has it evolved over the last decade in the digital age and the application of new technologies? What changes are taking place or will take place in the near future that will keep concrete in the forefront?
Richard McGrath: [Before we started] you mentioned the use of maturity embedded sensors in poured concrete. That is just one of the technologies being applied today more and more in the construction of our larger and more demanding concrete projects to reduce both labor and construction schedules. One of the biggest innovations that I have personally been involved with over the last decade is the introduction of Portland Limestone cement by the Canadian concrete industry. This reduces our emissions from both the fuels used in the manufacture of the cement and in the calcination reaction process in the limestone itself. We are reducing greenhouse gas emissions by 10 per cent with the manufacture and the use of Portland Limestone cement.
Nothing gets into the marketplace or into the industry until it’s approved by relevant standards. And we have just recently standardized ultra-high performance concrete manufacturing in Canada. We expect to see more use of ultra-high performance concrete that is incredibly durable and allows us to construct concrete structures in the most aggressive environments while providing the longest service life possible. This is certainly an advancement that has gone from being an ultra-specialized product to now being more mainstream.
We are also improving with every code cycle the economics of our concrete mix designs by recognizing finer grading of aggregates, which reduces the demand for cement in concrete mixes. This improves environmental sustainability while providing the same quality concrete. We are also adapting to the use of higher strength reinforcement for reinforced concrete that allows us to improve the constructability of these buildings and to utilize more economical concrete designs for our most demanding design projects.
We were talking about prefabrication as being an innovation in the construction industry. Yes, in the future many more projects because of the constricted sites in highly dense urban areas will require more prefabrication than on-site construction. But this competency has been practiced in precast concrete construction and prefabrication for decades in Canada. This technology is reaching new heights as you have pointed out with the [27-story] Marriott Hotel in New York. And we also have on-site, precast tilt up construction that is being used extensively on both the east and west coasts of Canada.
We saw just recently the emergence of 3D concrete printing for residential housing in some applications. And although this isn’t currently recognized in our codes in North America, in the coming [code] cycles I would expect that they will recognize this new technology as well. There is also self-healing concrete. These are rich cement content mixes that are demonstrating some self-healing capabilities after cracks form. These cracks can heal themselves because of the additional cement in these mixes. It hydrates with any ingress of water and serves to seal the concrete.
In each code cycle there is developing an increased flexibility in our design capability for our structures. You are now seeing structures with inclined columns and spiralling facades of a more complex architectural nature. These never would have been possible years ago if not for the advancement in the computerized design techniques for concrete structures and in the capability of concrete to accommodate these increased design demands.
These are just a few of the advances in concrete technology that we have seen utilized in the industry and there are more to come no doubt.
The Wood vs Concrete debate: Cost of building tall.
How does concrete compare with tall wood structures in terms of project cost from a) start to occupancy as well as b) total life cycle cost? Have you looked at it in terms of what is the cost implications between concrete and wood for taller buildings?
First I would point out that many, if not all of the recent tall buildings are really not all-wood structures. There is a fair degree of concrete construction [in these buildings] to handle the heavy lifting. Anywhere you have a concentration of loads or high stress levels, invariably you will see steel connections or concrete employed to take these high stresses and high loads. So it’s relatively easy from an engineering point of view to hang a gravity-loaded frame off of these concrete cores such as you see in Brock Commons [at UBC] as just one example. All of the heavy lifting is done with the foundations and the podium level providing a solid base for the structure and all the lateral loads due to wind and earthquake are being resisted by the concrete cores. Now, you simply secure the wood framing back to the concrete core and let it support gravity loads only, removing any need for moment-resisting connections or torsional resistance. In other words, concrete is counted on to do the heavy lifting while the wood frame goes along for the ride.
That is the first thing. You are never going to see an all-wood, 12-story building in Canada, not from this next code cycle. The limitations that are recognized for tall wood buildings will limit solutions to six-stories in our high seismic zone if you want an all-wood building [including the core]. So your [all] CLT wood building will only be six stories in high seismic zones and no higher than ten-stories in the rest of Canada. For fire safety purposes, the code will permit 12-stories, but they will all be hybrid structures where you’ll see concrete elevator cores, stairwells, and podiums supporting the gravity frame wood in these structures. Any all-wood building design greater than 10 stories will fall outside the scope of the 2020 NBCC and will have to be approved as an alternative solution by the authority having jurisdiction.
Adam Auer. I think that in terms of cost it is difficult to say since most of the taller wood buildings, six stories and up, have been underwritten at least in part through federal and provincial subsidies. So there aren’t enough of them yet to determine what the cost comparison will be at the end of the day. But it certainly seems at the moment that these buildings cannot be built unless they have at least some support from government funding.
Richard: That is an interesting fact. When the proposals were being made at the National Building Code level, the proponents failed to recognize that all of these projects demonstrating the capability of the material had been subsidized projects and there was no cost savings. In fact, in many instances there were cost premiums being paid to build these structures. They never would have gone ahead had it not been for the subsidies provided.
Are you aware of the Japanese architect Ban’s proposed 17-story condominium tower in Vancouver? It will have 2-storeys above ground podium and a core in concrete and the top 15 stories will be wood with exposed mass timber framing on the top six stories. It also uses concrete curtain wall panels on the first six stories hung on the wood frame.
Richard: That’s an interesting observation. As you see in most of these structures concrete is used for not only the foundations but the first couple of floors. That gets the wood component of the structure up and out of the high exposure area and the damage prone zone, not only from the environment but from impacts around the structure or damage by fire . It just improves the durability of the structure by getting the most vulnerable component up and out of the way of the high hazard areas.
One of the issues raised around wood structures is that it requires higher maintenance than concrete in areas associated with material deterioration from water, rot, insects, etc. Do you see these as valid concerns that haven’t been fully resolved?
In the latest code cycle – I’ve been at it for 37 years with the association – everybody was talking about the speed of construction and how much cheaper it was going to be. Nobody was talking about improving the building envelope on these structures to make sure that you didn’t have any moisture ingress. It is very interesting that many of our first high-rise wood projects are being built in British Columbia, which as you know is a jurisdiction that suffered from some of our worst serviceability construction losses in Canadian history. As a condo developer, I would find it very difficult to rush to adopt this line of construction in this perilous region of the country in regards to wood frame construction.
The argument is made that one advantage to wood is it takes less time to construct a wood structure. While this may be so onsite, how does the timeline look when the off-site fabrication of components is added? Alternatively, Marriott Hotels has started construction on a 27-story hotel in New York using prefabricated concrete modules that will go into place completely finished in 90 days (not including foundation and two story podium). Can/is concrete module technology thus already competing with wood in this area?
You are exactly right. There is greater emphasis being placed on this form of construction as constriction increases for on-site construction. One of the advantageous attributes of concrete construction is that you can modularize the construction process so effectively. I could look back to Habitat 67 in Canada and all the design innovations that it brought to the world stage. Habitat 67 was one of the first attempts of modularized residential construction here in Canada. While it didn’t take off at that time, its time may have come, and if projections are accurate, more structures will be built in the future using this design concept.
The Marriott hotel is a more recent example, but the beauty of this form of concrete construction is that these living units can be constructed and assembled in climate controlled factory conditions with all of the services built in. All of the services and finishes are embedded in the concrete. Concrete construction, as you know, facilitates embedment of services within the structural frame protecting it from all elemental deterioration as well as providing a long service life. So the short answer to your question is “Yes.” This is a coming trend recognized by more than our industry and we will see more of it. The concrete industry will continue to evolve and accommodate more and more of these types of building construction practices.
To read the original online article – CLICK HERE