Concrete Technology 2021
Greener Every Year and 35% Stronger
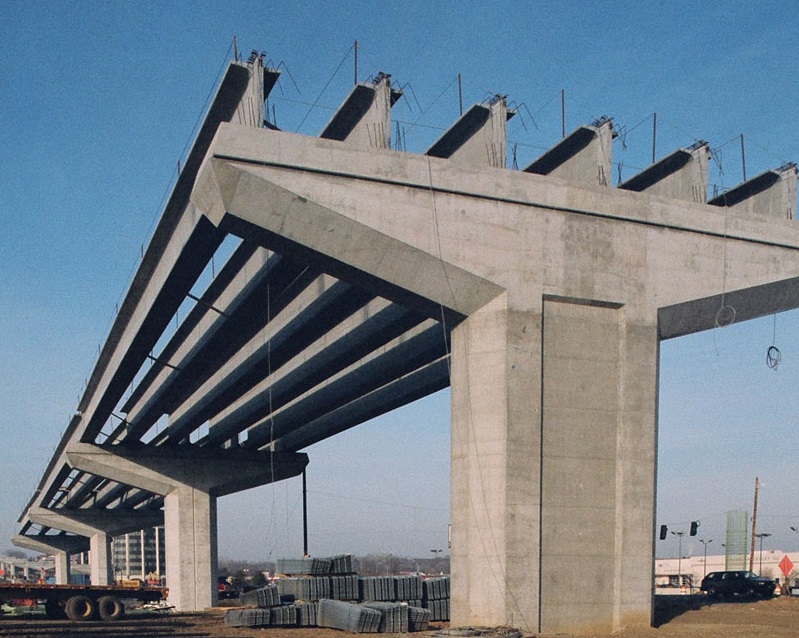
In our era of “carbon neutral” construction materials and green energy trends, the term “green concrete” has evolved to describe an environmentally friendly construction material.
The term “green concrete”, not so many decades ago, used to describe the condition of freshly poured ready mix concrete in construction projects or precast concrete products that required more curing time to achieve its full average 3,000 psi strength. The term “green” as applied to concrete was all about quality control.
Now, in our era of “carbon neutral” construction materials and green energy trends, the term “green concrete” has evolved to describe an environmentally friendly construction material.
Recycling and Concrete
Concrete is the most durable construction material in the world, and like the concrete used by the Egyptians to build the pyramids, an incredible 5,000-year lifespan for concrete structures isn’t unusual. But with the ever-changing demands of human civilization, the demolition of old obsolete concrete buildings and structures is inevitable.
But what can be done to dispose of the concrete rubble, a construction material with such incredible resilience to the elements that it’s not going to break down naturally in landfills any time soon? The answer is simple. Use the old concrete to make the aggregates for new concrete.
Fortunately, the crushing characteristics of hardened concrete are nearly equivalent to natural rock. That means that the original quality of the recycled material isn’t a factor, except for the poorest quality original concrete. As an aggregate for new concrete, the recycled rubble actually has advantages. Since all the original aggregate components are there as well as the existing hydrated cement paste, recycled concrete aggregates add more to enhance binding and strength characteristics than virgin crushed rock and sand alone.
With over 70% of the world’s population living in structures that contain concrete, the most natural disaster-resistant building material available, only one other substance on the planet is consumed more by human society. That substance is water.
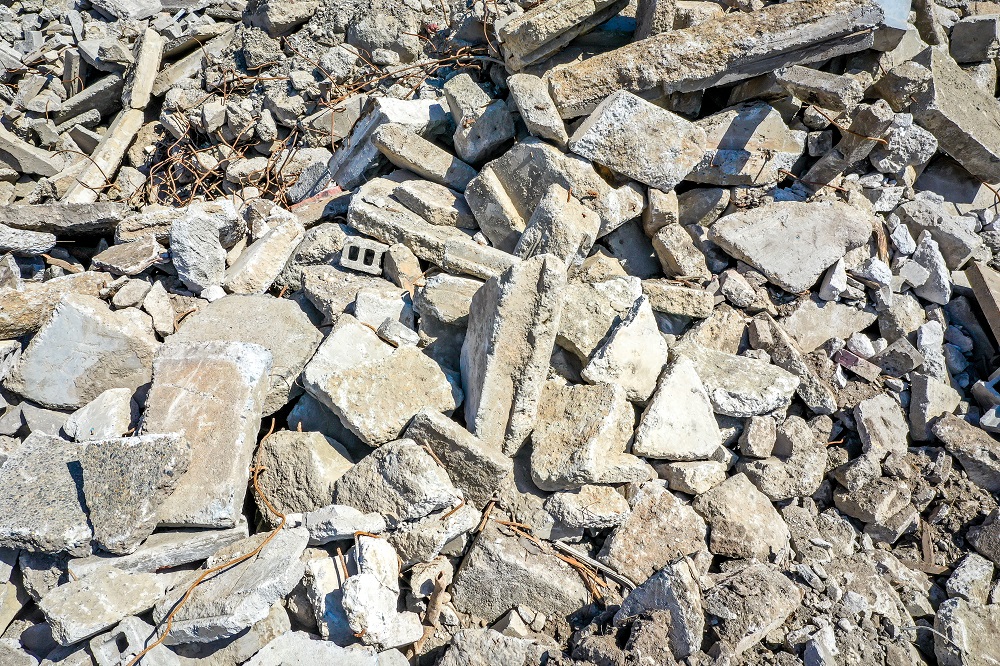
Under increasing environmental pressures, diverting concrete waste from landfills is another top priority for the industry.
New Research
In the US more than 55,000 miles of highway are paved with concrete. With such widespread use, scientists are constantly looking for innovative ways to make concrete even more resilient by increasing strength and heat resistance with new additives and aggregate enhancements.
Now scientists from Australia’s RMIT University may have come up with a win/win solution in the search for better concrete construction materials with a new recycled concrete aggregate that’s a superior choice for paving those 55,000 miles of highway.
In his informative January 2021 article at New Atlas Nick Lavars reports on how RMIT research has led to the addition of recycled rubber tires and concrete demolition rubble in the traditional time-proven concrete formula of portland cement, sand, crushed rock, and water. First developed for paving, the RMIT team is now moving on to develop the innovative recycled concrete formula for precast concrete products.
Arcosa Specialty Materials provides Gypsum Dihydrate and Gypsum Anhydrite to the largest cement manufactures in the nation. Our sister company, Arcosa Aggregates, has concrete recycling facilities.
To view the original article – click here